ID 700
Finance and Accounting Training Courses
Course : Auditing Supply Chain Management
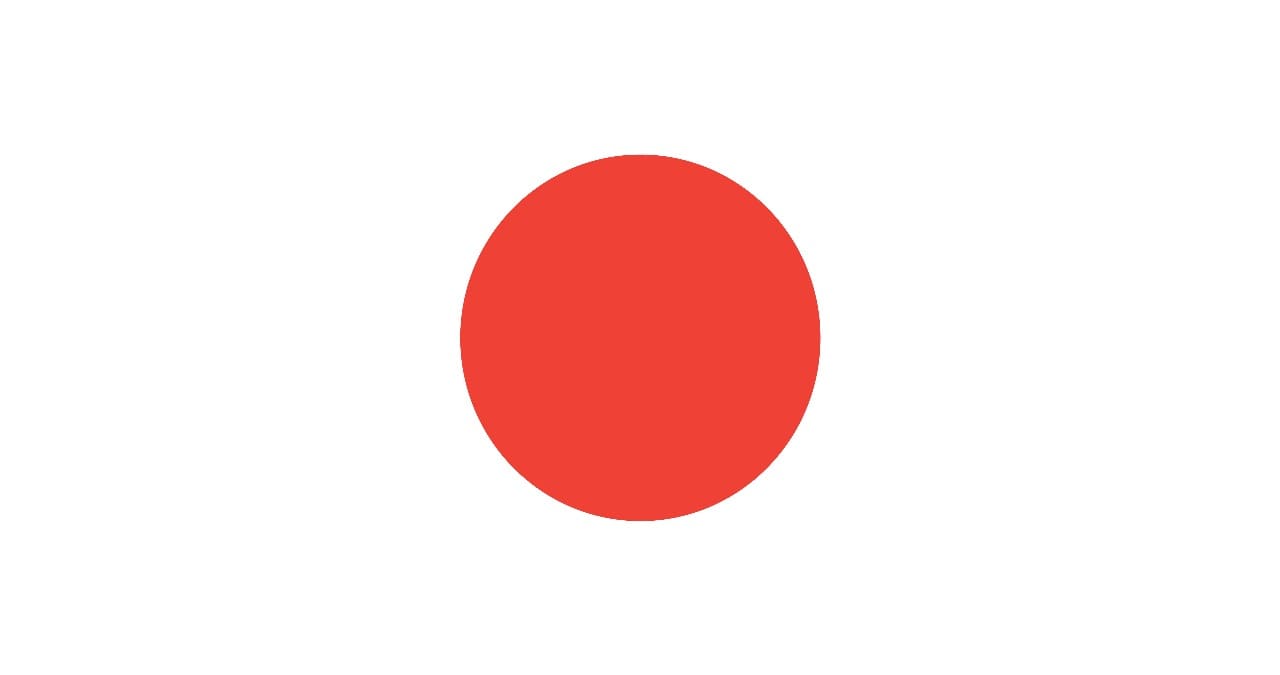
Tokyo
Hotel Name
Hotel Meeting Room
15 Sep 2025 : 19 Sep 2025
25 Hours
5950 USD
ID 700
Finance and Accounting Training Courses
Course : Auditing Supply Chain Management
Tokyo
Hotel Name
Hotel Meeting Room
15 Sep 2025 : 19 Sep 2025
25 Hours
5950 USD
Training Details
The management of the flows of materials, finished goods and related information to maximize the value of these activities for suppliers, companies, resellers and final consumers is vital for success in today’s fast-moving and cost-conscious economy. Organizations must coordinate operational and strategic activities across all business functions within and outside the enterprise to improve long-term performance and meet customer needs. This can only be achieved by using a total systems view of the relationships in the chain and making sure that all the parts work together efficiently and effectively. The resulting cost reduction, speed and perception of value differentiates world-class companies from those that struggle under the weight of unnecessary expenses, movements, bottlenecks and handling.
In this seminar you will learn about the units within organizations that are linked upstream and downstream to provide the products, services, information and finances from the source to end-user customers. You will also learn about the management of this chain, the planning and management of all activities involved in sourcing, procurement, conversion and logistics management, in addition to the coordination and collaboration that must exist between suppliers, intermediaries, third-party providers and customers. By focusing on business objectives, risks and leading practices that define essential control activities, internal auditors will acquire the skills to confidently audit their supply chain activities.
Senior Auditors; Internal and External Auditors; Audit Managers
Fundamentals of Internal Auditing (OAG101), Auditing the Manufacturing Process (OAP231) or equivalent experience.
Day 1 - Asset Cost Management Introduction
Maintenance & Reliability Best Practices are critical for every successful individual and company. This workshop delivers many practical and new Maintenance and Reliability Best Practices concepts and tools. You will discuss these concepts and practice using practical tools in case studies and discussion groups. The costs associated with equipment downtime and reduced production can be significant. Learning how to effectively manage all aspects of your industrial facility is a must.This workshop is a combination of instructor lead topic areas and class discussions. Interactive discussions will allow you to hear and learn best in class applications relating to maintenance planning and cost management strategies. You will have the opportunity to ask lots of questions in order to consider how best to apply these tools and techniques in your organization.
Day 2 - Laying the Groundwork
Maintenance & Reliability Best Practices are critical for every successful individual and company. This workshop delivers many practical and new Maintenance and Reliability Best Practices concepts and tools. You will discuss these concepts and practice using practical tools in case studies and discussion groups. The costs associated with equipment downtime and reduced production can be significant. Learning how to effectively manage all aspects of your industrial facility is a must.This workshop is a combination of instructor lead topic areas and class discussions. Interactive discussions will allow you to hear and learn best in class applications relating to maintenance planning and cost management strategies. You will have the opportunity to ask lots of questions in order to consider how best to apply these tools and techniques in your organization.
Day 3 - Applying the Value based Process
Maintenance & Reliability Best Practices are critical for every successful individual and company. This workshop delivers many practical and new Maintenance and Reliability Best Practices concepts and tools. You will discuss these concepts and practice using practical tools in case studies and discussion groups. The costs associated with equipment downtime and reduced production can be significant. Learning how to effectively manage all aspects of your industrial facility is a must.This workshop is a combination of instructor lead topic areas and class discussions. Interactive discussions will allow you to hear and learn best in class applications relating to maintenance planning and cost management strategies. You will have the opportunity to ask lots of questions in order to consider how best to apply these tools and techniques in your organization.
Day 4 - Ensuring the Continuity of the Value-based Process
Maintenance & Reliability Best Practices are critical for every successful individual and company. This workshop delivers many practical and new Maintenance and Reliability Best Practices concepts and tools. You will discuss these concepts and practice using practical tools in case studies and discussion groups. The costs associated with equipment downtime and reduced production can be significant. Learning how to effectively manage all aspects of your industrial facility is a must.This workshop is a combination of instructor lead topic areas and class discussions. Interactive discussions will allow you to hear and learn best in class applications relating to maintenance planning and cost management strategies. You will have the opportunity to ask lots of questions in order to consider how best to apply these tools and techniques in your organization.
The European Quality of Training and Management Consulting relies on advanced methodology in developing skills and enhancing the effectiveness of human resources. The company adopts modern methods to achieve these goals. In order to achieve its objectives, European Quality follows the following steps in a precise and professional manner:
European Quality Training and Management Consultancy of Training and Management Consulting reserves the right to change the location of the training program, change the accredited lecturers for program delivery, hold, or cancel the program in line with the companys vision and program conditions and our quality policy.
European Quality Training and Management Consultancy is certified
ISO 9001-2015
Course Options